Metal Building Trim Roll Former Drip Edge Trim Roll Forming Machine
Capabilities of the Metal Trim Machine Metal Building Trim Roll Former Drip Edge Trim Roll Forming Machine
**1. Roll Forming:
- The core function of the metal trim machine is roll forming, where metal coils are gradually shaped into the desired trim profile through a series of rollers. This process ensures precision and uniformity in the produced trims.
**2. Cutting:
- Equipped with hydraulic or mechanical cutting systems, the machine can cut trims to the exact length required. This capability ensures clean, accurate cuts that maintain the integrity of the trims.
**3. Punching:
- Some metal trim machines come with integrated punching systems, allowing for the creation of holes or slots as needed for specific trim designs. This adds functionality to the trims and expands their application range.
**4. Customization:
- The machine can be adjusted to produce various trim profiles and dimensions, providing the flexibility to meet unique project requirements. This customization is crucial for projects with specific aesthetic or functional needs.
**5. Material Handling Table:
- Capable of processing different materials such as aluminum, galvanized steel, and stainless steel, the machine offers versatility in production. This capability allows manufacturers to cater to diverse market demands.
Types of Metal Trims Produced by the Machine
**1. Edge Trims:
- Used to finish the edges of metal panels, providing a clean and professional look. Edge trims also protect the edges from damage and weathering.
**2. Corner Trims:
- Designed to cover and protect the corners of structures, corner trims enhance both the aesthetic appeal and durability of the construction.
**3. Drip Edges:
- Installed at the edge of roofs, drip edges direct water away from the fascia and the underlying structure, preventing water damage.
**4. J-Channels:
- These trims are used around windows and doors to hold siding in place and provide a finished look. J-channels also help channel water away from openings.
**5. Z-Flashing:
- Used in conjunction with siding, Z-flashing directs water away from seams and joints, preventing water infiltration and damage.
**6. Base and Cap Trims:
- These trims are used at the base and top of panels to provide a neat finish and protect the edges from moisture and damage.
Technical Data:
Items
|
Specifications
|
|
Material of coil
|
Material Thickness
|
0.4 mm-1.2 mm galvanized steel
|
De-coiler
|
Weight
|
3 ton manual
|
Forming system
|
Rolling Speed
|
10-15m/min
|
Roller Stations
|
About 9 stations forming
|
|
Roller Material
|
Cr40 Steel with quenching
|
|
Shaft Material
|
45# Steel Diameter 60mm shaft
|
|
Maim Motor Power
|
5.5 kw
|
|
Hydraulic cutting Power
|
4 kw
|
|
Cutting
system |
Material Of Cutting
|
CR12 with quench treatment
|
Hardness
|
HRC58-62
|
|
Tolerance
|
+-1.5mm
|
|
Electrical control system
|
Electric Source
|
220V, 60HZ,3 phase
|
Control System
|
PLC Control
|
|
Weight
|
About 3 tons
|
|
Way Of Drive
|
1 inch single chain
|
|
Size of machine
|
Length 5500mm* Width 600mm* Height 800m
|
Machine List:
3 ton passive de-coiler
|
1 set
|
Main roll forming machine
|
1 set
|
Cutting device
|
2 sets
|
PLC Control box
|
1 unit
|
Hydraulic station
|
1 unit
|
Output table
|
1 unit
|
Safety cover
|
1 unit
|
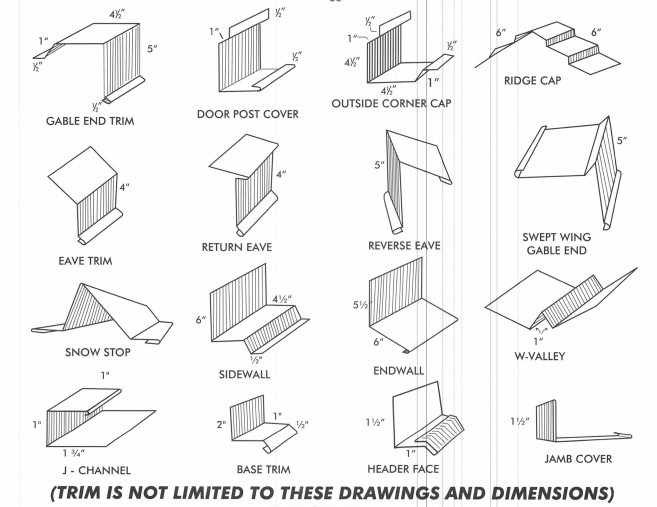
ZTRFM can also produce other kinds of Trim Roll Former Metal building manufacturing equipment Metal Rollforming Systems Roll forming machines Metal panel roll Former Metal roofing roll Former Roll forming metal, any request, welcome to contact us.
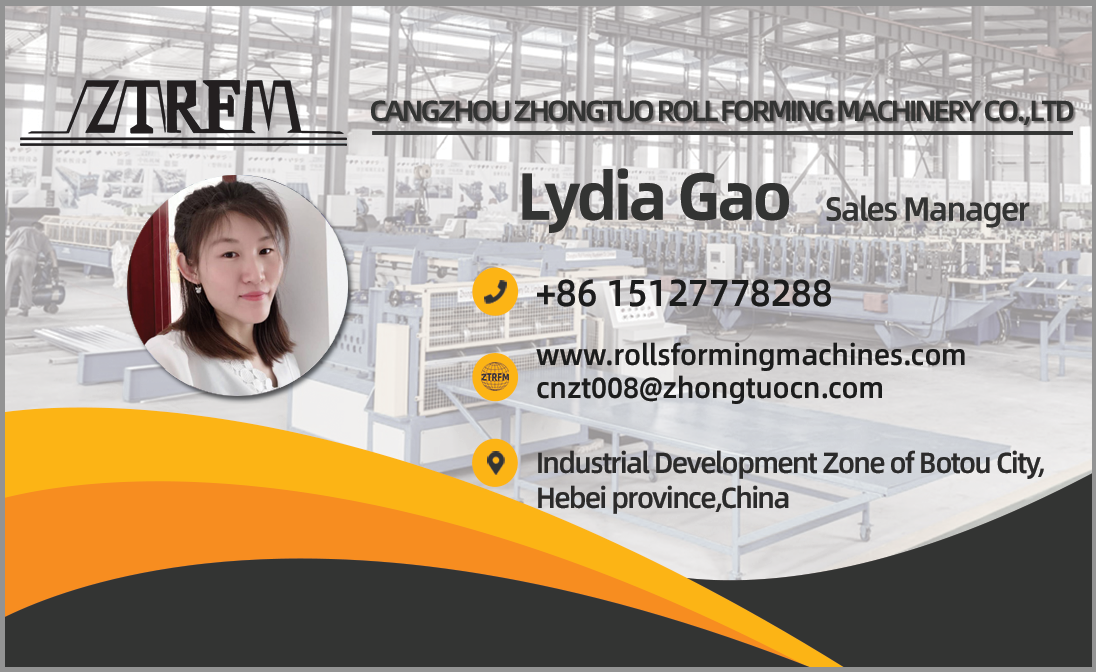