Automatic Solar Panel Framing Machine Photovoltaic/PV Bracket Roll Former
Features and Advantages of the Photovoltaic/PV Bracket Roll Former
The Photovoltaic/PV Bracket Roll Former (strut channel roll forming line) is specifically designed to produce C-shaped brackets with pre-punched holes, widely used in photovoltaic support systems.

The Photovoltaic/PV Bracket Roll Former efficiently manufactures various rack profiles by utilizing spacers or a cassette quick-change unit, allowing for fast and easy profile adjustments. The entire production line is operable by a single worker, ensuring convenience and efficiency.
The Photovoltaic/PV Bracket Roll Former employs PLC centralized control to seamlessly manage the uncoiling, leveling, feeding, punching, roll forming, cutting, and discharging processes. Multiple product lengths and quantities can be pre-programmed for automatic production, with remote control capabilities enhancing its operational flexibility.
Advantages of the Solar Bracket Roll Forming Machine
- The solar bracket production line is designed to produce high-quality solar PV supports with increased efficiency.
- Features a user-friendly PLC control system for automated operation.
- Equipped with Gcr15 rollers treated through a quenching process, achieving a hardness of HRC 60-65.
- Incorporates a tracking cutting system with Cr12 cutting blades.
Flow Chart:
Uncoiler —– leveling —– Punching —- Roll Forming —- Cutting —- Exit Rack

The Solar Bracket Roll Forming Machine Profile Drawing:
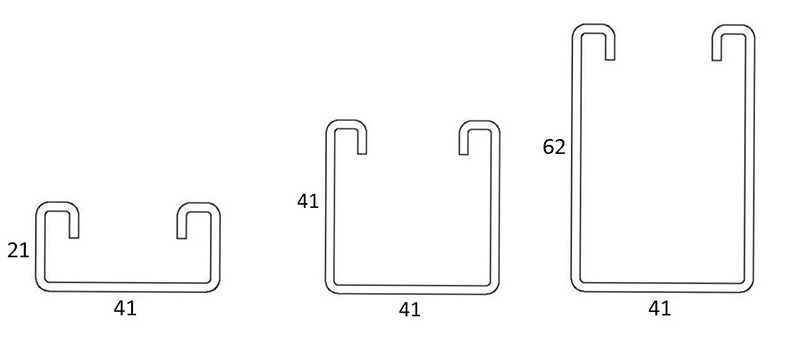
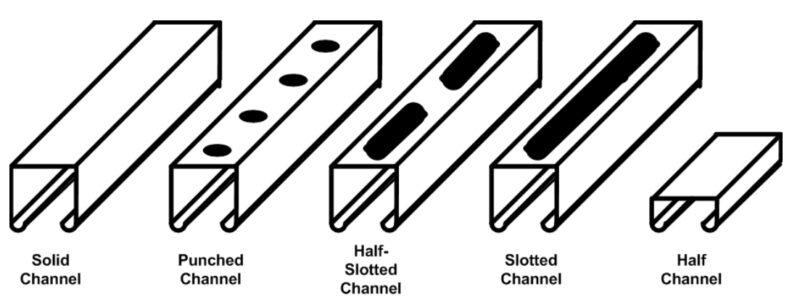
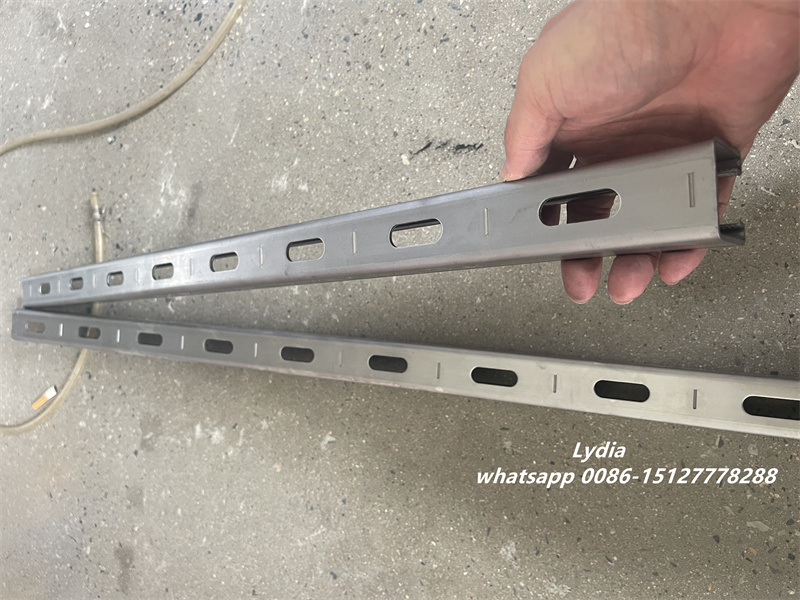
The Technical Specifications Of the the Solar Bracket Roll Forming Machine:
Series | Details | Parameter | Comment |
Material | Raw material | Galvanized steel | Customer confirmed |
Material thickness | 0.5-2 mm | ||
15 holes punching mold | |||
Speeds: | 45 times /min, 8-10 m/min | ||
Include punching mold: | mold material SKD-11 | ||
Roll forming machine |
Guiding device | Placed on the machine by seller | |
Rolling shaft material | 40 Cr with tempering treatment | ||
Shaft diameter | 80 mm | ||
Roller material | Gcr15, some are Cr12 HRC 56-58 | ||
Rolling station | 18 stations | ||
Work speed | 45 times /min, 8-10 m/min | ||
Machine structure | Vertical memorial arch frame | ||
Machine basic frame | Cast iron mold frame (very strong frame) | ||
Bearing | Chinese famous brand Harbin | Famous brand of Harbin | |
Work power | 5.5kw*2, 7.5kw*2 | ||
Transmission | Gear box transmission | With cover | |
Safety cover | available |
More detailed pictures of the machine:
Feeding table
1.Function:Put the sheet into the machine
2.Benefits:Can ensure the sheet smooth and flat
3.Hand knife:Can save material
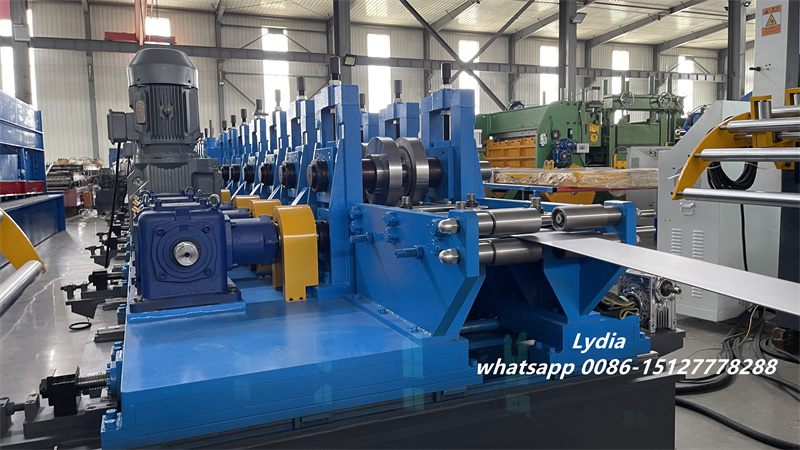
Chrome treated shaft and wheel
The Chrome-treated shaft and wheel for our roll forming machine ensure exceptional durability and smooth operation. The chrome coating enhances resistance to wear and corrosion, prolonging the machine’s lifespan and maintaining consistent performance.
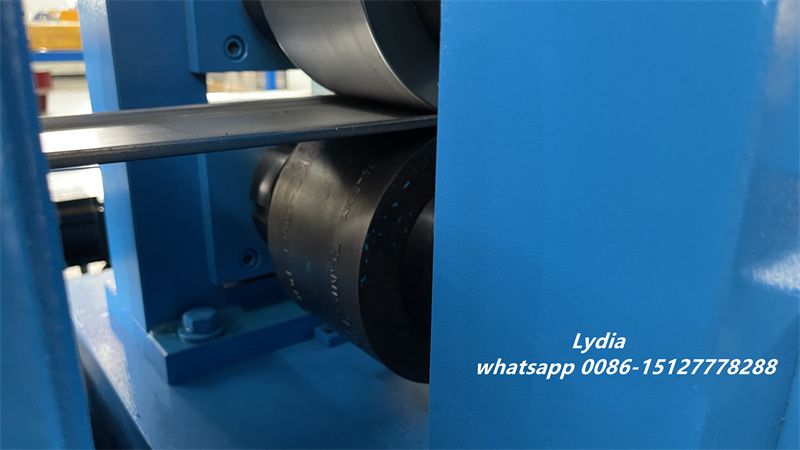
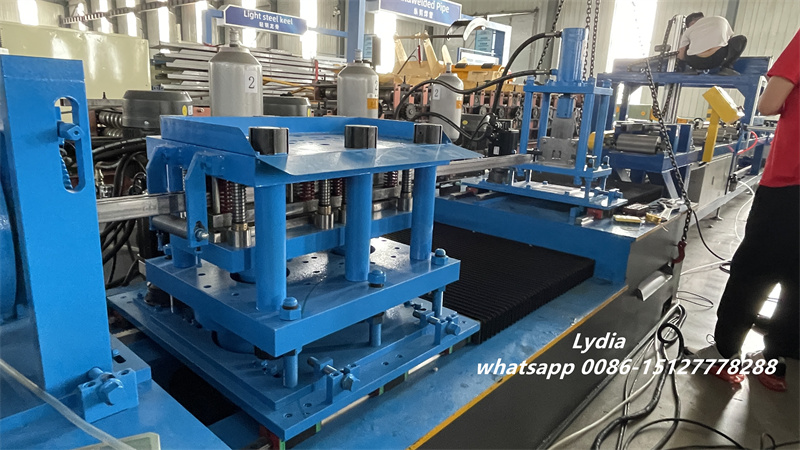
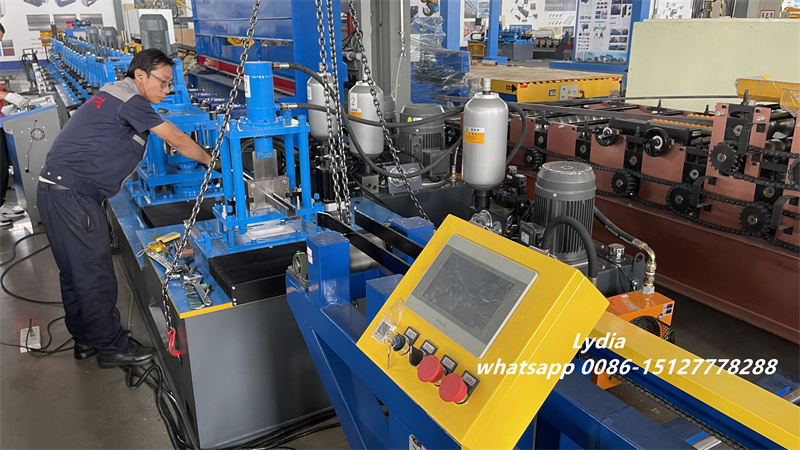